Quite accurately, we can say that in this field, the concept of constant improvement is applicable. Based on the views of people, firms seek to improve satisfaction, eliminate variation, and improve productivity. At the heart of this quest lies a powerful approach: Lean Manufacturing is one of the most popular current theories about managing organizations.
If the above practices are adopted, then the outcome that will be realized by manufacturers is quite impressive. But let me go directly to what I believe is at the heart of Manufacturing Excellence and look at how Lean can work.
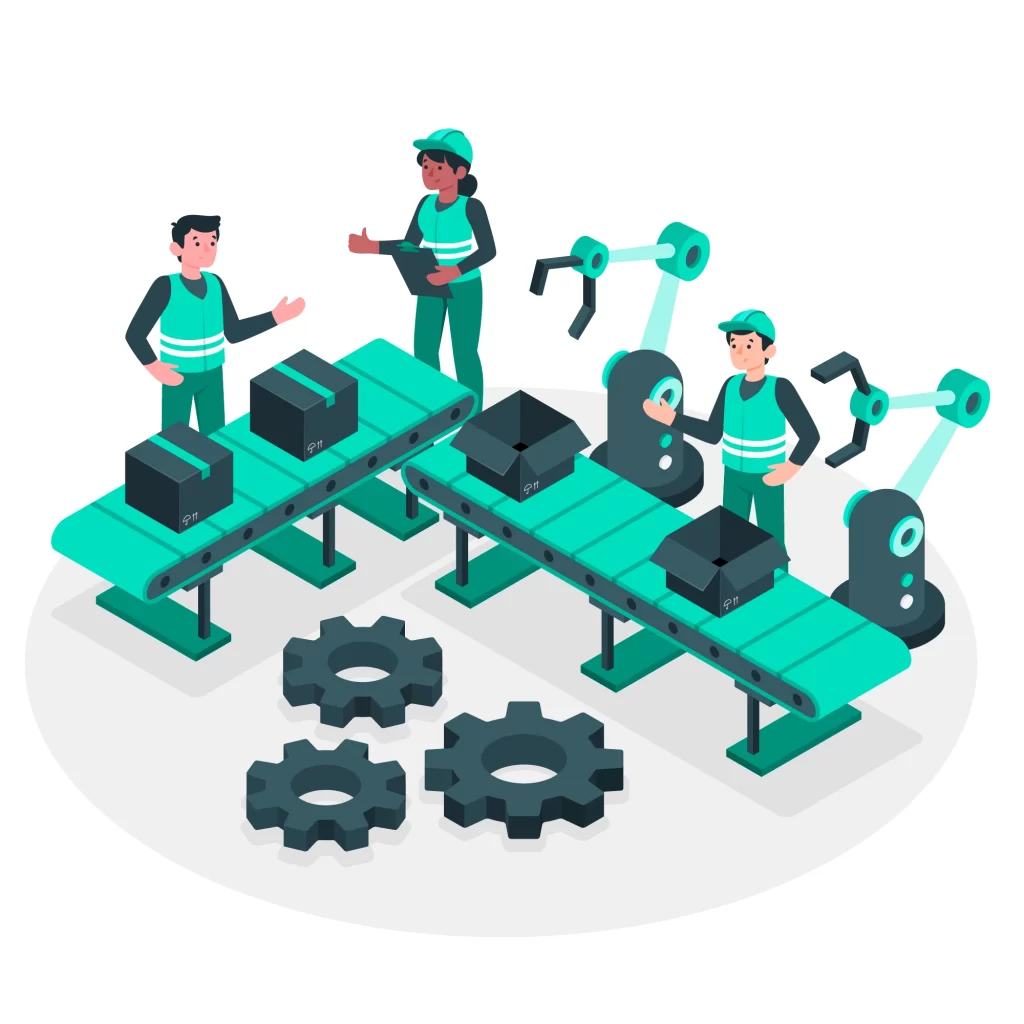
Understanding Lean Manufacturing
Lean manufacturing is an umbrella that provides for the elimination of waste, creating instead more value for customers. It was introduced in the Toyota Production System but now it is a widely used method. Lean thinking focuses on integrating changes, focusing on people, and a problem-solving methodology.
Principle of the Lean Manufacturing
- Value: Define what aspects make the customer’s value. As a rule, anything that is not regarded as having value is regarded as waste.
- Value Stream: List down all the activities that occur in the production line. This assists in the visualization of wastes and therefore comes up with ways of eradicating them.
- Flow: Make sure that it is not interrupted during the process of production. Get rid of bottlenecks in order to increase effective efficiency.
- Pull: Introduce a pull system of manufacturing where the production is done in line with the consumers demand. This leads to a reduction of overproduction, or in other words, a reduction of stock that may take time to sell.
- Perfection: Principle of improving on what is foreseen as the attempt to reach the goal even if it has not been achieved perfectly is highly recommended. Applying it, furthermore, supports constant evaluation and optimization of processes by the teams.
The Power of Lean Manufacturing
- Reduced Waste: Lean manufacturing is all more about reducing waste when it comes to materials, time and even labor. This results in reduction of cost and thus an enhanced profitability.
- Increased Efficiency: Standardized means lead to shorter time spans for development. In essence, this means quick delivery turnaround time and satisfied customers.
- Improved Quality: – Lean culture makes it possible to maintain quality. It makes workers take their responsibility more seriously thus improving their output.
- Employee Engagement: – Lean speaks for organizing teamwork and those very elements which make people cooperate with each other. Employees who are engaged show more commitment towards their duties and responsibilities.
Implementing the Lean Principles
Therefore, there is a need to plan about the change to the Lean manufacturing environment. Here are some best practices for successful implementation:
- Start with Leadership Commitment: The following concept is particularly essential in Lean management; Leadership is a critical factor in the promotion of Lean activities. It is important that leaders of the institution pass across the message of Lean and the value of attaining this profoundly. They make great commitments that form the basis of other commitments within the entire organization.
- Train Employees: It is pertinent to invest in training programs that will educate the citizens on Lean principles. Provide those employees with the skills and information required in order to successfully put the changes into use. This creates the culture of improvement in that organization.
- Map the Value Stream: Ensure you do value stream mapping. List: All of your activities that you have within your production process ranging from your input to your output. Show all the areas that have a problem with waste and what can be done to optimize it.
- Engage Team: Ensure that Lean process improvement activities engage everyone within the organization. A best practice to adopt is to ensure that they give word their views and recommendations. Not only does it increase the level of commitment but also it reveals good ideas.
- Implement Kaizen Events: Kaizen, which literally translates as ‘change for better, ‘ refers to gradual changes for the better. Schedule Kaizen events to target certain areas so that specialists can work on them individually. They can produce great payoffs such as identified in the collaborative sessions.
- Measure Progress: It is necessary to define measurable goals and objectives and set key performance indicators (KPIs) to use them in the process of evaluating results. These metrics should be revisited frequently, to examine the changes brought forth by Lean projects. It also allows one to make necessary changes with regard to strategic direction in order to remain on track.
Common Lean tools and techniques
There are several tools that can help to implement the Lean concept and to make the Lean transformation. Here are some of the most effective:
- 5S Methodology: 5S belongs to the house of Lean and it comprises 5 S’s that are Sort, Set in order, Shine, Standardize and Sustain. It also helps to create order and tidiness in working places. It is easier and safe to work in a clean environment hence performance in work delivery is improved.
- Kanban: Kanban means a mode of operating that uses visual boards. Doing that helps in managing the workflow of products to be produced and the stocks that are available. It has also been observed that the use of a Kanban board makes it simpler to determine how far one is in the process and what the issues could be that slow down the process.
- Value Stream Mapping: On the basis of a generally linear flow of materials and information, this tool offers a graphical representation of the primary process. It assists in the assessment of possible wastage and potential for making improvements. Value stream mapping is very important when it comes to understanding the end-to-end process.
- Root Cause Analysis: If any complication occurs due to the implementation of a particular system then one needs to know the cause. Tools such as the ‘5 whys’ are used to gain more insight into problems. This means that solutions are directed at solving the real issues on the ground.
- Standard Work: Standard work defines exactly how that particular work is to be done, so as to be most effective. It minimizes variance and brings about order. It is however important to write down standard procedures because organizations need documents to train and to ensure quality.
Challenges in Lean Implementation
However, it is essential to point out that there are pros associated with Lean, but coming with cons while being implemented. Here are some common obstacles and how to overcome them:
- Resistance to Change: A lot of employees are likely to oppose change because of fear or lack of adequate understanding of change. Feedback especially when it is negative should be dealt with an openness. Illustrate to them the benefits to be derived from Lean implementation and engage them in the process.
- Lack of Training: It is also important to ensure that all employees within an organization understand Lean practices as poor application through lack of adequate training may lead to more catastrophic results. Ensure that your organization provides thorough training of all the teams to ensure that they are well fortified in all the areas.
- Inconsistent Leadership Support: Lean projects are a continuous process hence need constant support from top management. Ensure that there is constant communication of the progress made with affirmation of achievements in the process.
- Short Term Focus: A lot of organizations tend to manage with regards to short-term outcomes as opposed to sustainable development. Many students already carry around this idea of sustainability and what they should and should not do in terms of other practices as well. Continuous improvement is not for the short term only but a long-term process which may be compared with marathon races.
Lead in Practices: Success Stories
- Toyota: Toyota is one of the most outstanding manufacturing companies in the world, and it originated the Lean concept. Thus, the continuous management’s commitment to efficiency improvement and elimination of waste has rated the company well in the automobile industry.
- Boeing: This is in light of the fact that Boeing sought to apply Lean principles to increase production effectiveness. The company managed to decrease delivery time for its aircrafts due streamlined processes and evident decrease of waste.
- Intel: Intel adopted Lean in an effort to increase the efficiency of its chip-making process. As for the third one, the company has been able to cut on the cycle times and embraced quality techniques hence satisfying the customer fully.
Embracing Digital transformation
It is, therefore, noteworthy that the use of digital tools can augment Lean processes by offering real-time information. This centers on the experience that through analytics, organizations can easily detect wastes and enhance the decision-making aspect. The adoption of technology will complement the Lean journey.
Sustainable and Lean
This means that sustainability is slowly finding a place in manufacturing processes. It is important to note that lean principles are complimentary with sustainable practices. When it comes to sustainability, it is crucial to lower the amount of waste a company produces and increase productivity at the same time.
Conclusion: Lean Manufacturing
Lean Manufacturing is a process leading to the transformation of an organization or organization process through the deployment of Lean principles. Thus, implementing these practices can provide the desired results for the organizations. He noted that the advantages of working with Lean include the minimization of waste, enhanced productivity, and better quality of the product.
FAQ’s
Mainly, lean principles go in that they center their efforts on adding value for the customer while reducing valuelessness. It comprises value identification, value stream mapping, flow, pull and perfection.
It’s an intensive, short-terminitied process change intervention to attack a defined process improvement issue. It promotes ‘team synergy’.
Lean manufacturing practices consume less resources through making the manufacturing process efficient and with less waste. This in line sustainability with goals and helps in reducing the impacts on the environment.
Also Read: Biotechnology: The Future of Medicine and Agriculture
Responses (0 )